Nanoparticle based resistive strain gauges are paving the way for flexible touch screens. Researchers from the Nanotech research group at INSA Toulouse have investigated the electromechanical behavior of such strain gauges, fabricated from arrays of colloidal gold nanoparticle (NP) wires, using synchrotron radiation on the SIXS beamline. Microstructural changes within these NP wires under uniaxial stretching are correlated to their macroscopic electrical resistance variations. Their work, published on the Nanoscale review, suggests a linear longitudinal extension and transversal contraction of the NP wires with applied strain (0 to 13%).
The unique optical and electronic properties of colloidal nanoparticles (NPs) assembled on different substrates have been exploited for various sensing applications. In particular, these systems are attractive for sensing gases, (bio)molecules, temperature, mechanical deformations, and for photodetection. Among these, nanoparticle-based resistive strain gauges have excited much interest during the past few years. Such sensors, fabricated from colloidal NPs assembled on flexible substrates by different techniques such as airbrush spraying, layer-by-layer deposition or convective self-assembly, indeed exhibit high sensitivities. Despite their promise, studies pertaining to such sensors have so far been largely rudimentary. A clear understanding of the macroscopic electromechanical behavior of NP-based strain gauges calls for an evaluation of the strain induced dynamic changes at the nanometric scale. A relevant method to perform this evaluation is small angle X-ray scattering (SAXS), or in grazing incidence (GISAXS). SAXS has been previously used to monitor the self-assembling process of NPs or to evaluate the packing and organization of the NPs within assemblies. However, the NP mechanics at nano-scale governing the performance of a NP-based strain gauge remains unexplored.
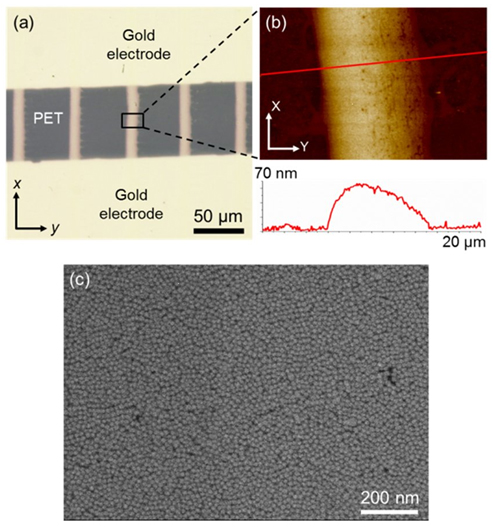
Figure 1 : (a) Optical microscopy image of the active area of a typical strain gauge based on parallel wires of 15 nm gold NPs on PET (polyethylene terephthalate) substrate, connected between two gold electrodes,(b) Top-view AFM image and associated cross-section of part of a typical NP wire and (c) SEM image showing the NP organization of the topmost layer of the wires.
An innovating Strain gauge
A typical strain gauge is presented on figure 1. It consists in wire shape NP assemblies, deposited onto polymer substrates between two gold electrodes. Gold NPs, with a diameter chosen between 5nm and 21 nm were used. NP based strain gauges are resistive sensors wherein the distance between each NP is modified when the substrate is stretched, inducing a variation of the tunnel resistance between the neighboring NPs, and therefore an exponential resistance variation of the all NP assembly.
SAXS monitoring of the mechanics of nanoparticles
In the article, scientists report on SAXS and GISAXS investigations of nanoparticle-based resistive strain gauges in action, carried out to understand the key mechanisms underlying the performance of these sensors. The mean interparticle distance variations under uniaxial stretching estimated by SAXS and GISAXS are correlated to the simultaneously measured macroscopic deformation and the electrical resistance variations of the strain gauges, and the results are analyzed further using numerical simulations of electronic conduction.
Typical SAXS and GISAXS scattering patterns obtained using the SIXS beamline are shown on figure2. These patterns show multiple order diffraction maximum which can be attributed to scattering of NPs, showing the lateral and vertical organization of NPs and allowing monitoring the inter-particle distance variations. During uniaxial stretching, the circular ring visible on SAXS scattering figure is deformed giving an elliptic pattern. That pattern deformation evidence an inter-particle distance increase along stretching direction and a transversal contraction. Furthermore, a non-ideal adhesion of the NPs to the substrate has been measured.
All those experimental results give precise information on the mechanical behavior of NPs at nanoscale, allowing for more precise strain gauge numerical modeling, and for strain gauge optimization.
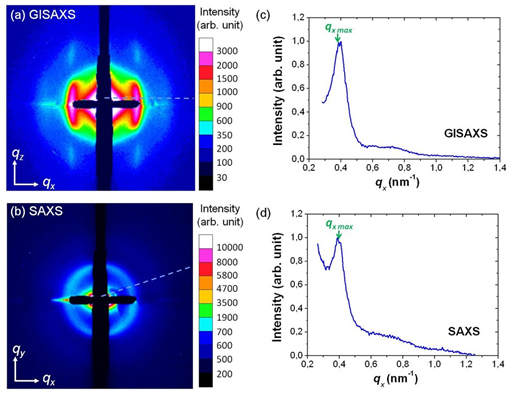
Figure 2 : Typical GISAXS (a) and SAXS (b) scattering patterns for unstrained gauges fabricated with 15 nm gold NPs, and GISAXS (c) and SAXS (d) profiles along the dashed lines, extracted from the scattering patterns